Granite Reimagined: Circular Innovations in Construction Materials
- Kshitija Mruthyunjaya
- Aug 26, 2024
- 3 min read
Updated: Aug 27, 2024
On our fieldwork journey through the granite supply chain, visiting quarries and processing units, we uncovered the staggering scale of waste generated. This eye-opening experience drove us to explore innovative solutions to transform granite byproducts into construction materials.
Written by Kshitija Mruthyunjaya and Shivangini Tandon
Over the last few months, we have been mapping materials available in and around Goa and Maharashtra to serve our sites in these locations. We considered transport emissions, supply chain systems, and availability and decided that we would aim to use materials available within 500 kilometres of our sites.
During this exercise we took a trip to granite quarries and processing units to understand the stone supply chain. What struck us the most during these visits was the quantum and kinds of waste generated at each stage of the granite supply chain. We saw first hand how the traditional industrial approach to 'extract-consume-waste-dispose' was leading to serious environmental and health consequences for the communities in and around these sites.

The granite supply chain generates a substantial amount of diverse waste at every stage, from quarrying to end-of-life disposal. This waste includes large-scale materials like overburden and waste rock, as well as finer byproducts such as stone dust and slurry. The process also produces various off-cuts, fragments, and broken pieces of different sizes. To put the scale of this waste into perspective, one of the companies alone generates approximately 1600 tonnes of slab offcuts every month when cutting smooth blocks out of raw stone blocks.

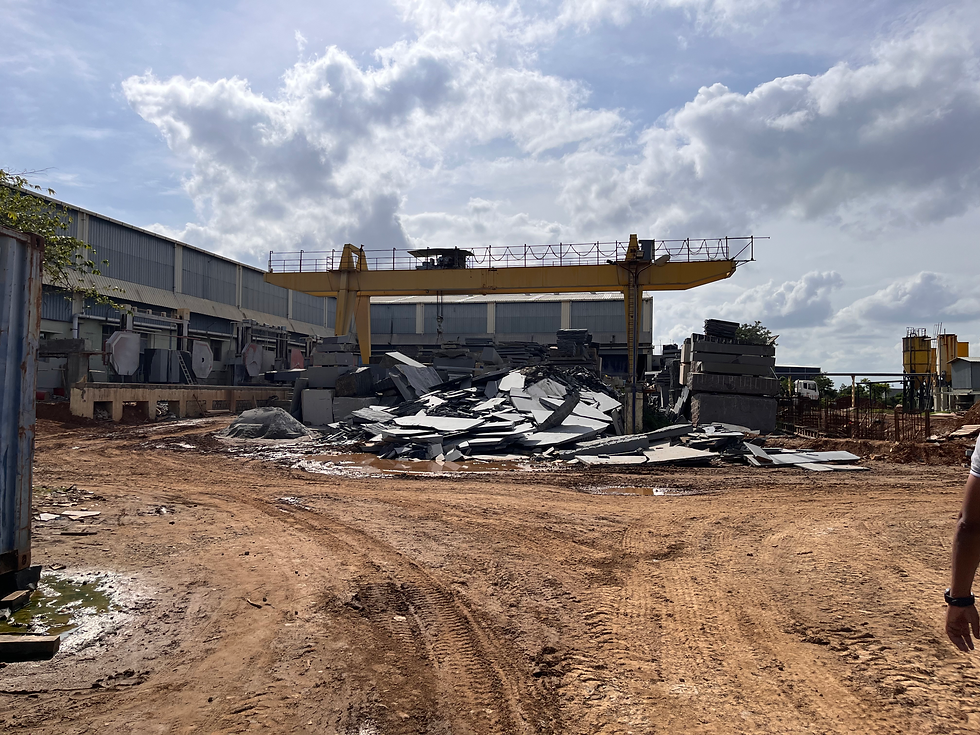
Additional waste comes from packaging, transportation emissions, and worn-out abrasives used in finishing. This wide-ranging waste stream presents significant environmental and health challenges, but also offers numerous opportunities for recycling, repurposing, and creating value-added products throughout the supply chain.


To address this problem of waste, our team at SPF has initiated a project to repurpose granite offcuts. We're adopting a circular economy approach, which aims to eliminate waste and maximise resource use by keeping materials in use for as long as possible. One of the companies we visited, God's Granites, was particularly eager to work with us on repurposing their waste. We began with a comprehensive evaluation of the material by our multidisciplinary team, including a material scientist, architect, and interior designer. Their initial assessment revealed that the thickness of the granite slabs might not be ideal for direct use as interior flooring.
However, this challenge sparked creative solutions. We identified several potential applications for these offcuts, including:
Terrazzo flooring
Landscaping elements
Cladding materials
Decorative composites
For our first experiment, we tested the waste to transform it into decorative plastering. Our in-house artisans took on the task of transforming these granite offcuts. They began by crushing the material into powders of varying granularity, which were then carefully sieved to achieve consistent particle sizes.
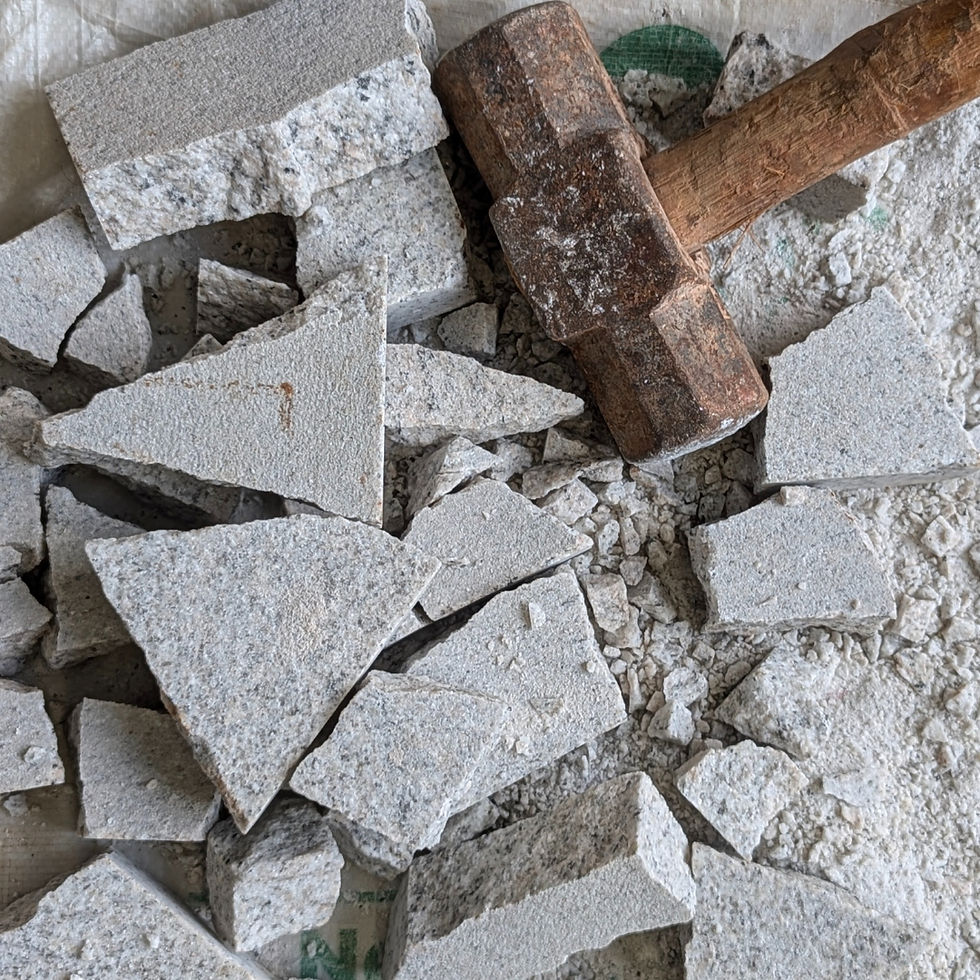
To create a usable plaster mix, the team combined the processed granite powder with a binder in a 1:3 ratio. Additional aggregates were incorporated to enhance the mixture's properties. The result was a unique, granite waste-based plaster that
could be used for various decorative purposes, effectively giving new life to what would otherwise have been dumped into landfill.



This experiment represents a practical application of circular economy principles in the granite industry, turning byproducts into valuable resources. Our hope is that this approach will also open up new possibilities for materials in construction and design.
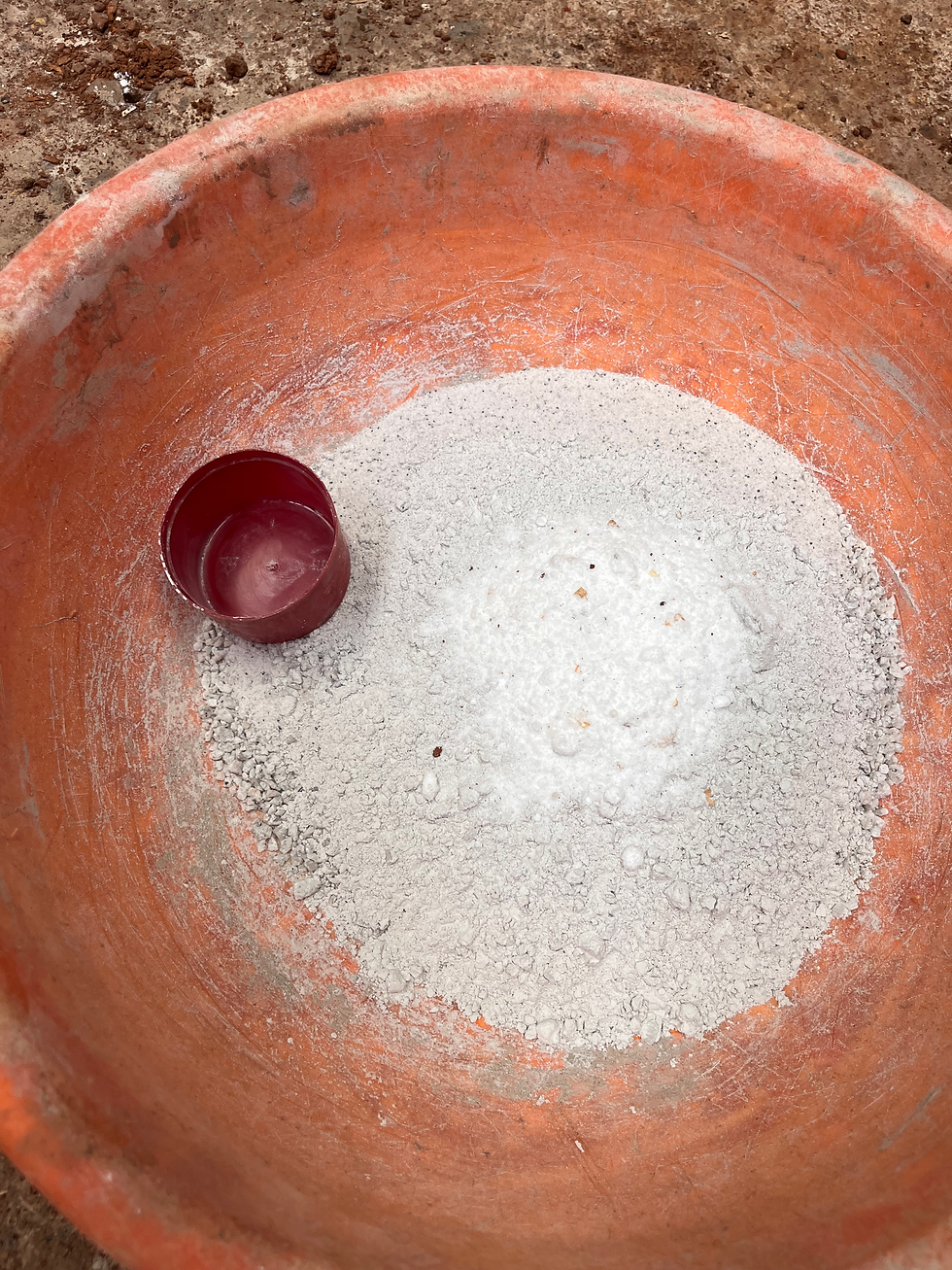

Credits:
We appreciate God Granite's support in this project.
Comentarios